Aluminum content is abundant, second only to oxygen and silicon. Metal aluminum and its alloy products have the characteristics of corrosion resistance, non-magnetism, high specific strength, and good thermal conductivity, especially aluminum alloys with light weight and large load capacity, which are widely used in aerospace, mechanical manufacturing, shipbuilding industry, and automotive manufacturing.
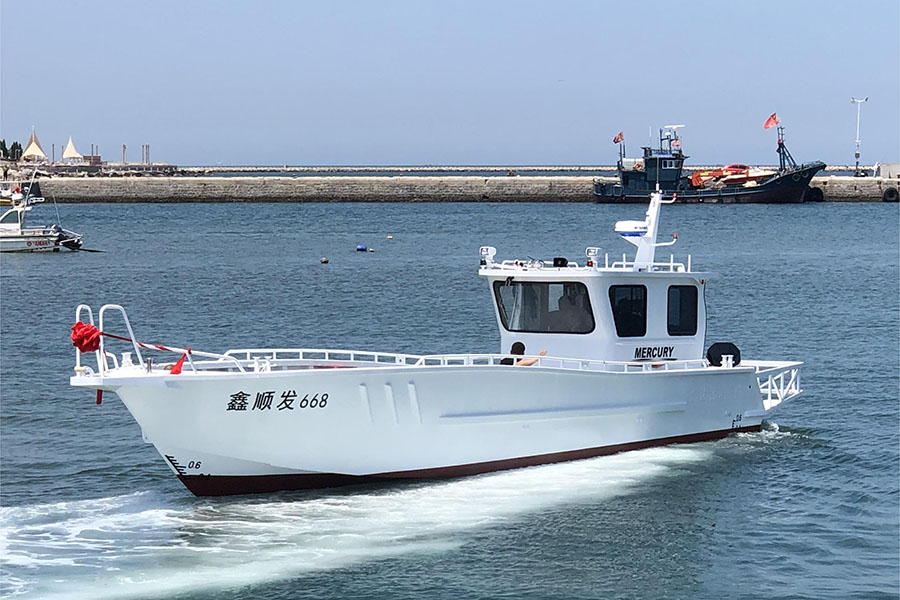
With the large-scale construction of high-end aluminum alloy boats, the market demand for aluminum alloy boats in areas such as passenger transportation, leisure tourism, and law enforcement in China is constantly increasing, which also brings good development opportunities to shipbuilding enterprises. Ships built with aluminum alloy have low energy consumption and fast sailing speed, especially in the construction of high-speed boats, which are widely used. But unlike other steel vessels, aluminum alloy high-speed boats have high design requirements, special requirements for process materials, welding, cutting, etc. Therefore, mastering the design and manufacturing process of aluminum alloy high-speed and fast boats has positive practical significance for improving the level of ship design and construction.
The welding of aluminum alloy ships is a key and difficult point in their construction. In actual construction, welding equipment with small deformation and high efficiency should be used. Common welding processes include automatic/semi-automatic argon arc welding (MIG) and tungsten automatic argon arc welding (TIG). In short, ship construction personnel are required to be proficient in welding processes and test conditions. In addition, shipbuilding enterprises need to prepare various equipment in advance for site and equipment preparation, as well as aluminum cutting, cutting, and margin correction.